曲げて、切って、プレスして。一枚の金属板が職人技で姿を変える
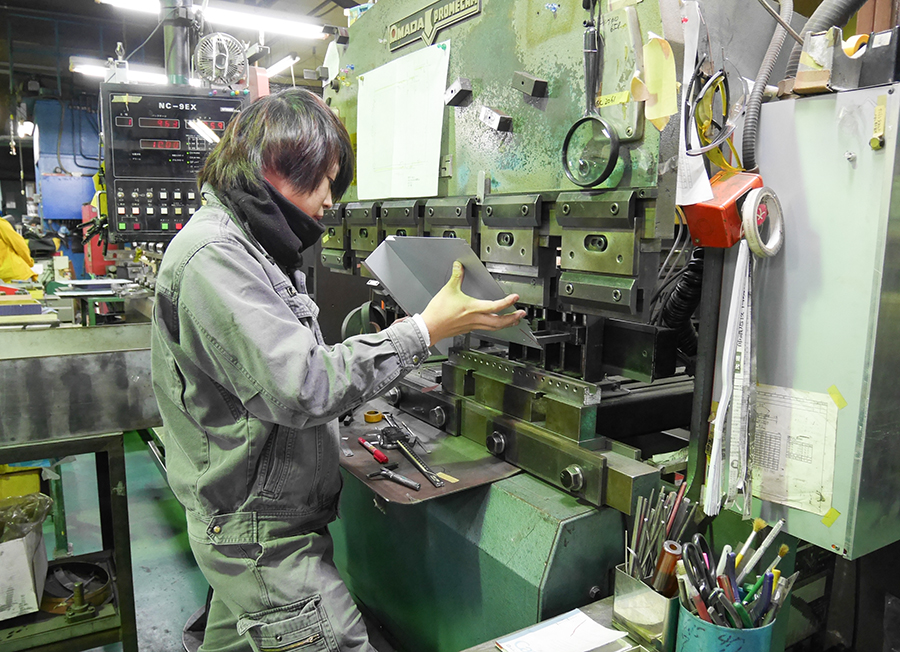
26歳から61歳(社長)まで在籍する職人たち。
豊里金属工業は、薄板状の金属板からさまざまな形を生み出す精密板金のプロ集団である。主に家電やIT機器、設備機械などを開発するメーカーが商品の「試作」に必要となる金属部品の成形加工を手がけ、量産体制に入る前の最終試作品に採用される。
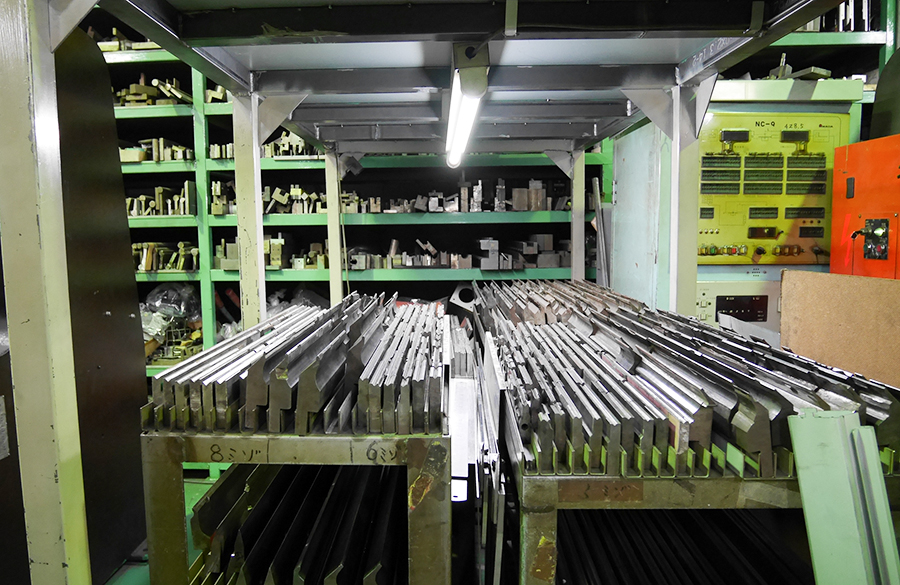
曲げ加工をするためのプレスブレーキに使用する金型は、曲げ角度や厚み等の違いによって膨大な数を揃える。
ガスコンロの部品やテレビのバックパネル、洗濯機やコピー機の内部など、さまざまな場所に用いられる金属パーツは、メーカーが多額の費用をかけて製品に合わせた金型を作り、大規模な工場で量産されている。その前段階で、設計図通り実際に部品を作り出し、組み立てて検証する作業が「試作」だ。
使われるパーツはオーダーごとに異なる為、加工工程を考え、機械を操るのも、すべてが人次第。職人の柔軟な考え方と技術、最新の大型機械の合わせ技が同社の持ち味だ。
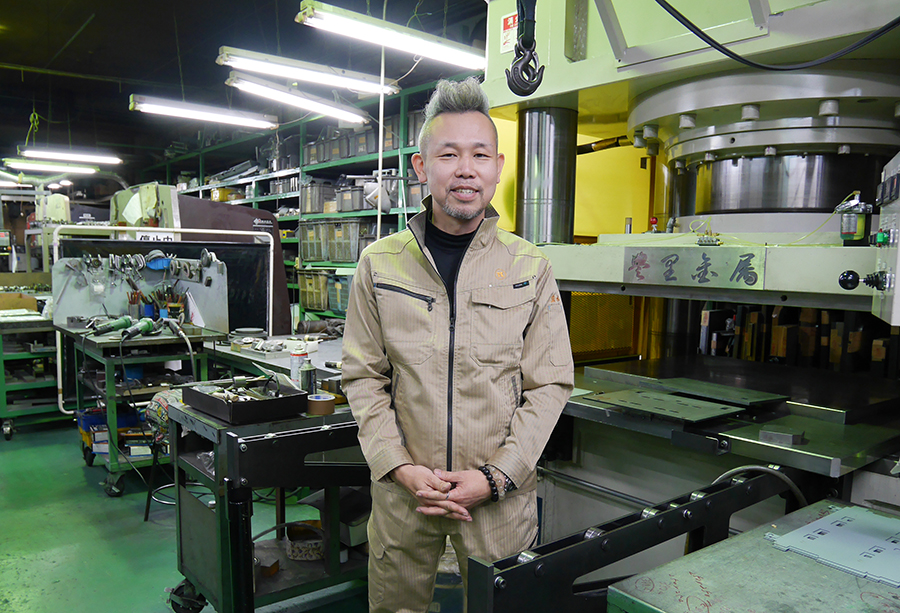
機械設計の職を経て同社で17年の工場長、岩水氏。背面にそびえるのは1000tの油圧プレス機。
得意とするのは、「絞り」と呼ばれる板材を立体的に加工する技術。凸型と凹型の簡易金型の間に金属板を挟み、プレスして成形する。金型作りには特に力を入れてきた。
厚みの違う金属板を何枚も重ねて製作する積層金型をベースに、レーザー加工機や電気を通して金属を切る、ワイヤカット放電加工機、複雑な曲線は3D切削ができる大型機械マシニングセンターを活用して必要な形に削り出す。これらのブランクや曲げの加工技術を組み合わせた「ハイブリッド簡易金型」を使用し、最高で1000tの圧力負荷が可能な油圧プレス機へ。
70インチTV用の大型パーツから、わずか1cmの中に10カ所以上の曲げ加工が入る金属片まで、月100〜200種類の「新製品」を作り出す。
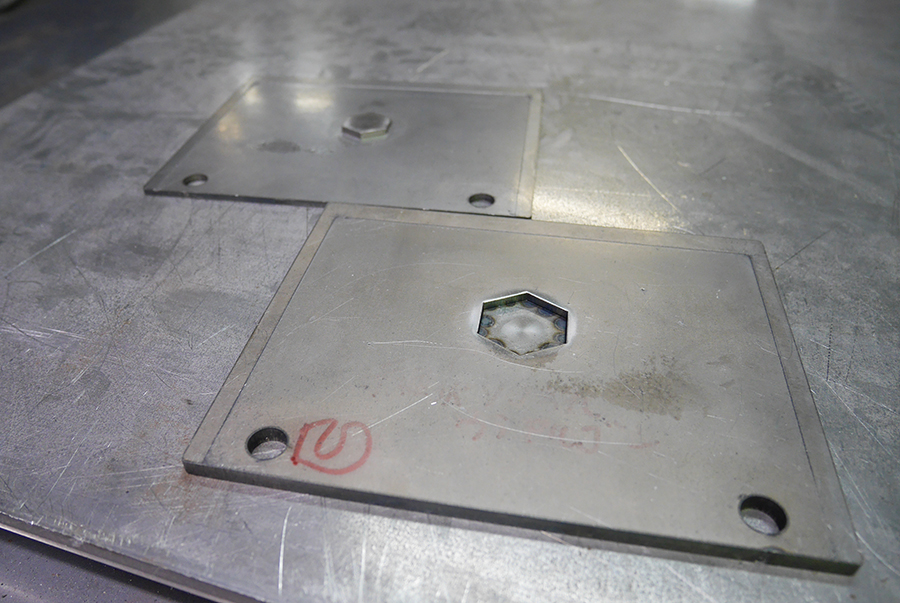
凸型と凹型の金型と、できあがった製品(写真右)。曲線は3次元にカットできるマシニングセンターで加工。
また、他社が断った案件や、依頼時点で納期が過ぎている案件の駆け込み寺にもなっている。「できないというのがイヤなんです」と工場長の岩水氏。スタッフ同士、それぞれが試したやり方をセッションする。
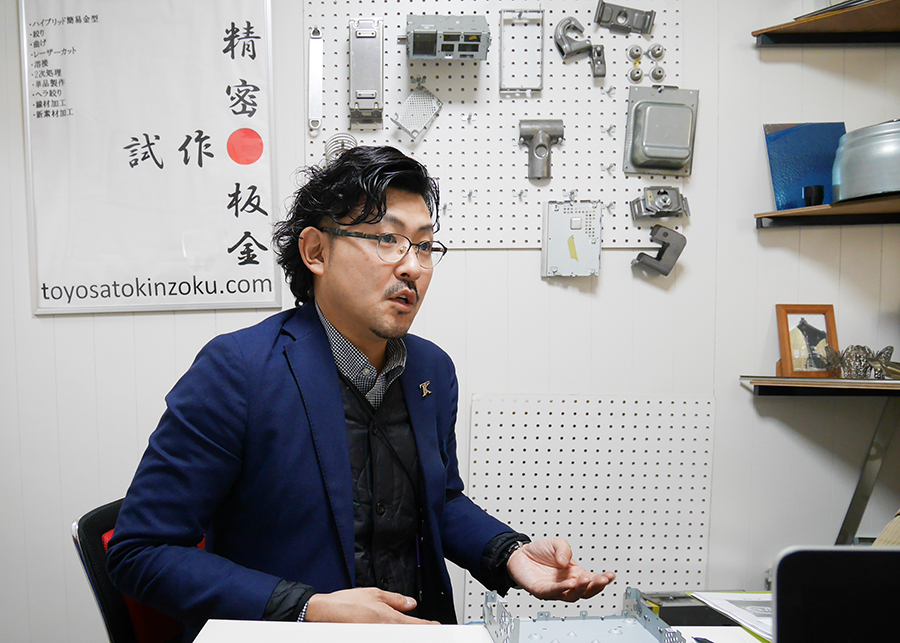
開発側の要望と職人技をつなぐ営業担当、小椋氏。新規顧客が増えるここ数年を支えてきたホープだ。
同じ金属でもロット等の違いで、厚みや加工のしやすさが変わってくるため、板材の厚さには100分の1ミリまでこだわる。板厚やプレス加重の変更、金型から作り直しなど試行錯誤し、量産体制を見据えて手順や素材、図面から提案することも。
「レベルの高い妥協点を見出すのは難しいですが、時間やコスト、形や強度など、求められている要素を優先して仕上げています」。
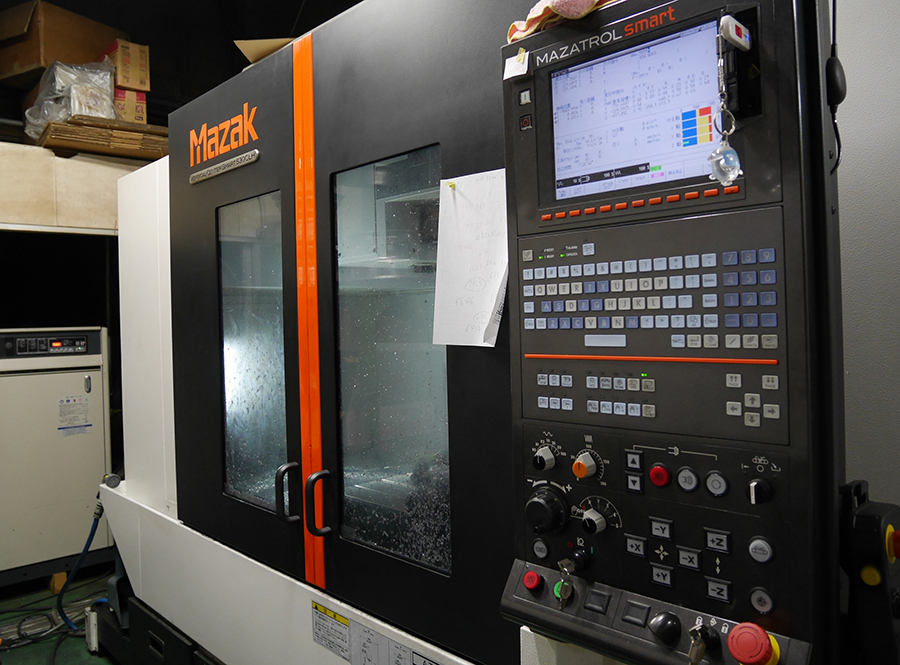
「大阪ものづくり優良企業賞」を受賞。中小企業支援の補助金で最新設備を導入し、自社でできることを増やしてきた。
最近は3Dプリンターの性能が向上し、取って代わられることも。大阪から開発拠点を移すメーカーもいる。それでも、毎年新しい機械を取り入れて、社内で完結できるように新たな技術を導入している。
オフィスや工場に置く什器や飾り、社章を金属で手作りするのも、技を磨くため。「板金加工の限界を知るまで、挑戦し続けます」。
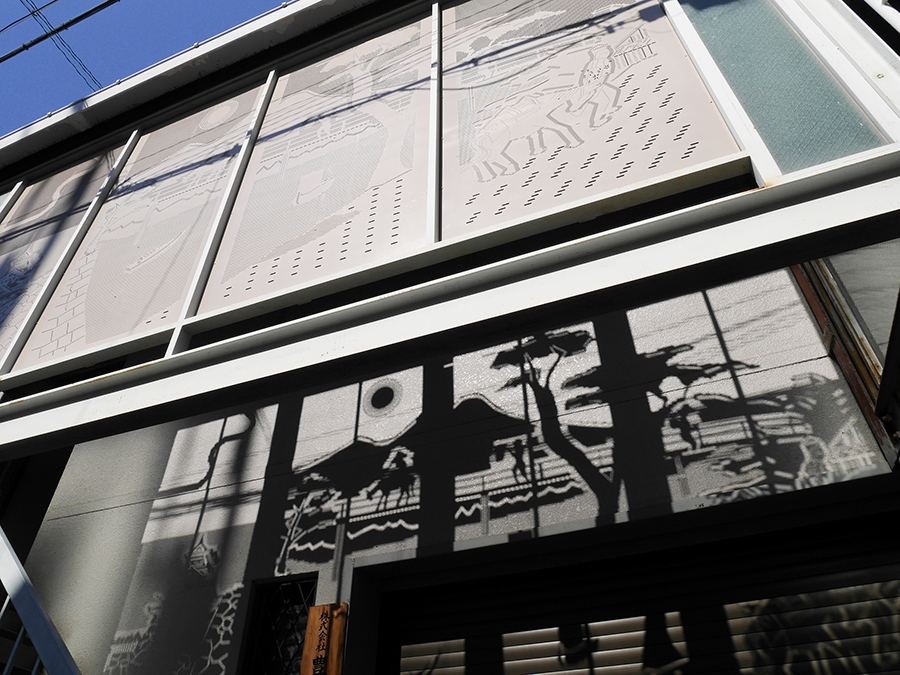
表玄関に掲げるパンチングメタル(タレットパンチプレス加工)は、光線の角度で模様が現れる。胸元の社章バッジ、資料ラック、果てはオブジェまで、高度な職人技と遊び心で自由にものづくり。
(取材・文/衛藤真奈実)