苦境で鍛え抜かれた工程提案力
自動車部品をはじめとする歯車の加工技術では他社の追随を許さない。汎用旋盤から5軸加工機まで約100台もの工作機械が並ぶ工場は壮観だ。歯車を製造する専用機械だけでも約20台を数える。さらに複雑な形状の加工については3Dによる設計・加工部門でカバーする体制を整えている。「自動車のマニュアルミッションならすべて社内で加工できるよう設備をそろえている。用途や品質、納期など顧客の要求に応じて最適な工程を選択し、提案できる」と繁原氏。こうした姿勢で「困ったときは繁原製作所に」という評価を確立してきた。
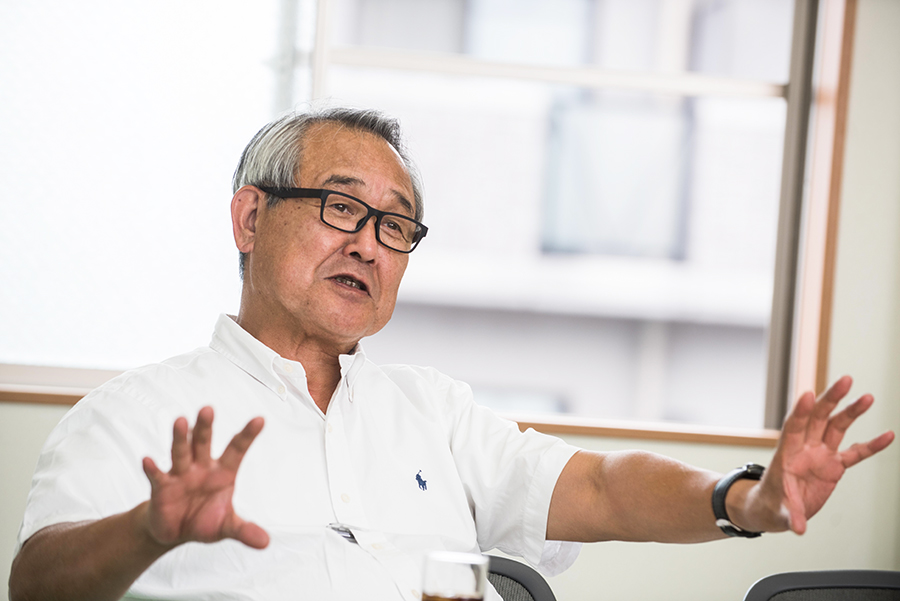
代表取締役社長の繁原秀孝氏。
37年前の会社設立当初は、自動車部品メーカーの下請けとして中ロットの量産部品を手がけていた。その後ほぼ10年ごとに3度、事業の谷に直面し、そのたびにより小ロットの高付加価値製品へ、短納期化へとチャレンジを続けてきた。
2度目の谷の後に挑んだのは「あらゆる加工を2週間で納品する体制づくり」だ。同社は30年ほど前からレース用自動車の部品づくりを手がけ、レースで露見したトラブル箇所を修正しては次のレースで確かめる繰り返しの中で技術を磨き上げてきた。レースの間隔は2週間。そのたびに加工に必要な治工具を造っていては間に合わない。そこで間に研磨工程を挟むことで加工時の精度を出し工程を短期化した。新しい加工プロセスはリスクを伴うが、併せて高度な測定器を導入することで顧客が求める精度、強度を実現させていることをデータで示し、納得を得た。
リーマンショック後の3度目の谷では、レクサスの最高級車に搭載するエンジンギアの製造にじっくり取り組む機会を得た。精度を極めるため数ミクロン単位で歯面を調整し、量産工場に求められる品質保証規格を単品工場で実現するという高いハードルが課された。部品の製造工程ごとにデータを取得し、いかに均質な精度が出ているかを証明することで関門をクリアした。
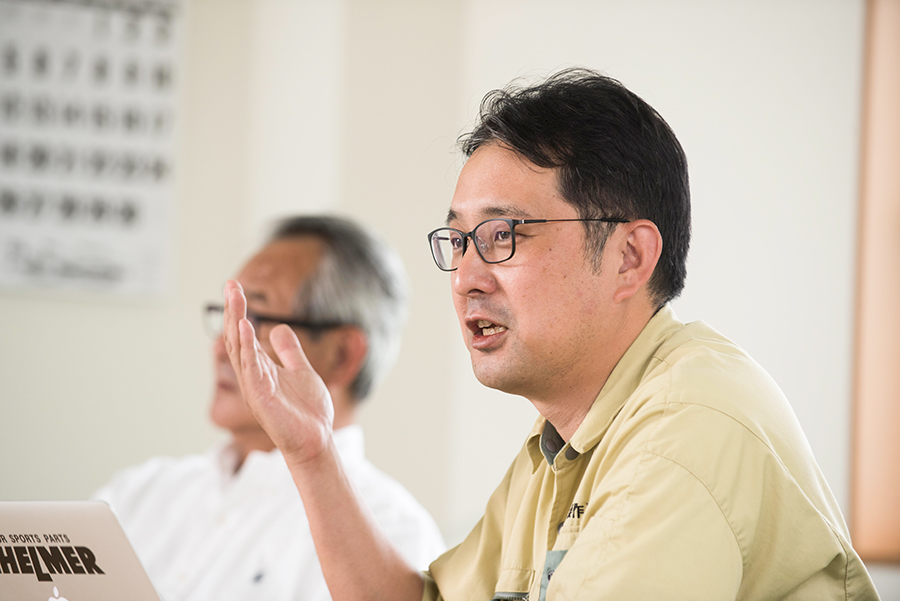
取材に対応してくれた取締役営業統括 繁原秀和氏。
入社後、技能者は工作機械、3D設計、検査の工程を全て経験する。毎年売上げの1%を人材教育にあて、技能検定の資格取得用に専用のフライス盤も導入した。団塊の世代の技能労働者が大量に退職し、今や大手メーカーでさえものづくりの技術の基盤を失いつつある。大手メーカーから直接、口座を開いてほしいという依頼が絶えないのも手づくりの技術が認められてのことだ。
今挑んでいるのが電気自動車向けの多段変速機の開発。電気自動車には「多段」は不要との定説に疑義を呈し、多段にすることでモーターの機能を補う発想で優位性が認められつつある。「設計図通りに造るのはだれでもできる。なぜそれが必要でどこが肝かを全体の中でとらえられるのがうちの強み」と、年間4000種類もの加工案件を受託する経験値は何物にも代えがたい。
(取材・文/山口裕史 写真/福永浩二)
★アンケートやってます★ぜひご協力ください★
https://www.sansokan.jp/enquete/?H_ENQ_NO=24049