創業100年以上、磨き続けた針・パイプ加工技術
ステンレスやチタンのパイプの周囲を叩きながら素管外径から0.3mm~3mm程度まで外径を細くしていくスウェージング(絞り)加工。加工に使用するダイスと呼ばれる半円の形にくりぬかれた二つの金型で、少しずつ回転しながら叩いていくことによって外径を均一に細くしていく。完成した細いパイプは、インクジェットプリンターでインクを吸引するノズルや医療用特殊針など用途は幅広い。

スウェージング加工で先端を絞った絞りパイプ。
工場内にはスウェージング機が40台ほど並んでいる。「それぞれの用途別に専用機をそろえているため、さまざまな要望にお応えできます」と中井氏。だが加工はそれだけでは終わらない。例えば、血液検査で血液を吸引するための特殊針は、スウェージング加工後、先端加工したパイプ切断面内部を顕微鏡でのぞきながら手作業で鏡面に磨き上げる。各種加工に使う穴あけ機、針先端を研磨する尖頭機などは自社で製造することで、ユーザーの細かい要望に応え、コストを抑えることができている。スウェージング加工を手掛ける企業は国内でも数えるほどしかいないが、使用する機械や治具を内製化できるのが有限会社森田製針所の強みだ。「困った時の最後の砦でありたい」と矜持をのぞかせる。
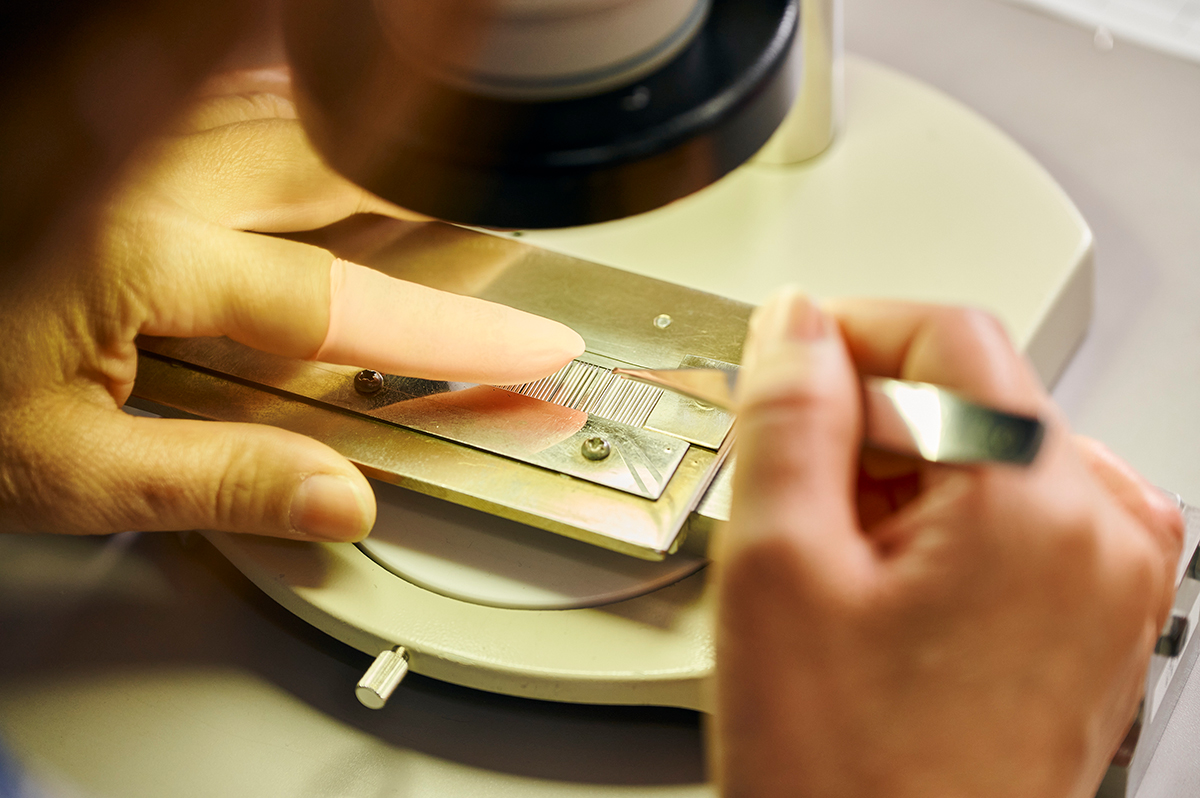
顕微鏡でのぞきながら、切断面の内部を磨く。
創業は1921年。メリヤスの編み針の製造でスタートした時点から100年以上スウェージング加工を手がけてきた。メリヤス針は1980年代に海外製に駆逐され撤退を余儀なくされたが、それに代わって点滴に使う針を医療機器メーカーから受注し、培った技術を他用途へと転用していった。2010年には大手半導体製造装置メーカーから半導体洗浄用ノズルの製造依頼を受けた。「元のパイプから細くする割合である減径率が非常に高いので割れやすく、苦戦を強いられた」と中井氏。1年後に量産がスタートしたものの歩留まりが改善されず採算が取れない状態が続いたが、試行錯誤を繰り返しようやく安定的に生産できるようになり、今では森田製針所の主力製品の一つになっている。
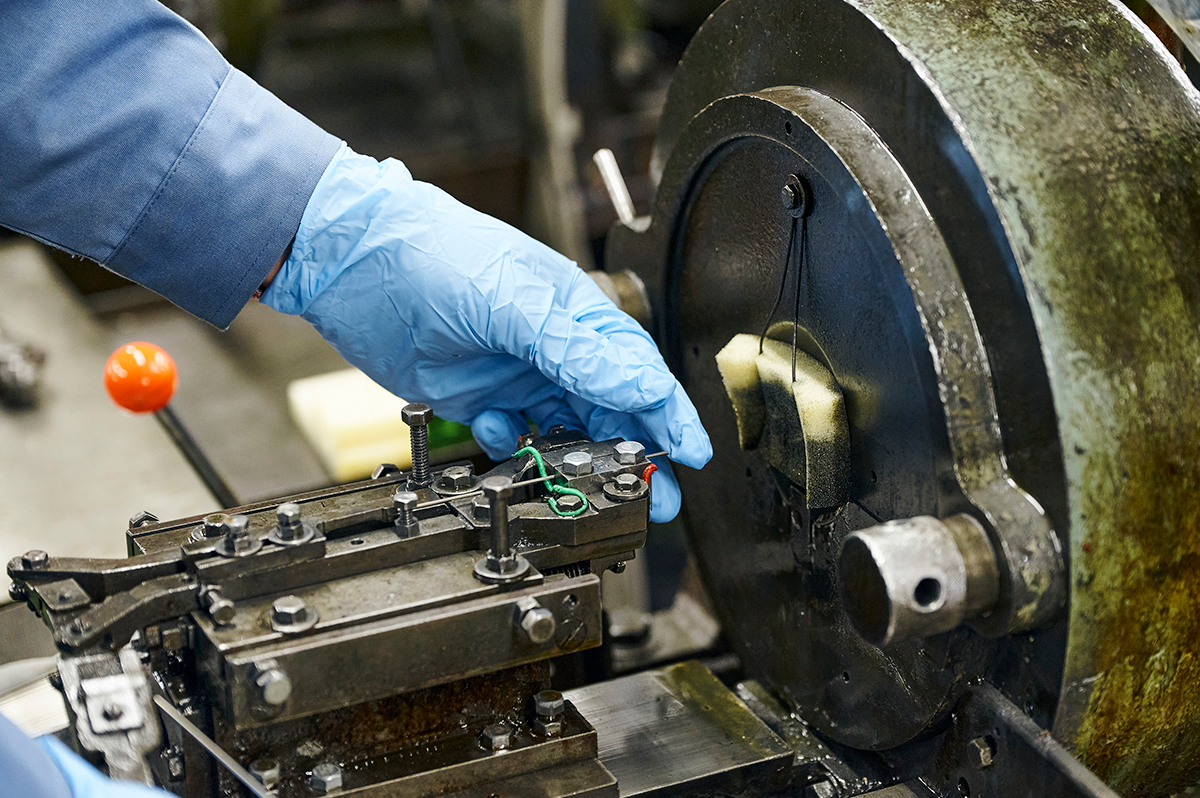
二つのダイスで叩きながらパイプを細くしていくスウェージング機。
パイプを送り出す速度、ダイスの製作や回転の速度などスウェージング加工には熟練された技術が必要なだけに技術の伝承は大きなテーマだ。「何がわかっていて、わかっていないのか」を正確に把握するため、工程ごとの細かなチェック項目を作成し、レベルを5段階で評価する「マルチスキル表」をつくり、「半年に1度個別面談で話し合いながら学んでいける環境を整えています」と中井氏。今後は医療分野に注力するとともに、未知の分野にも挑み、スウェージングを中心とした各種加工技術の適用領域をさらに広げていこうとしている。
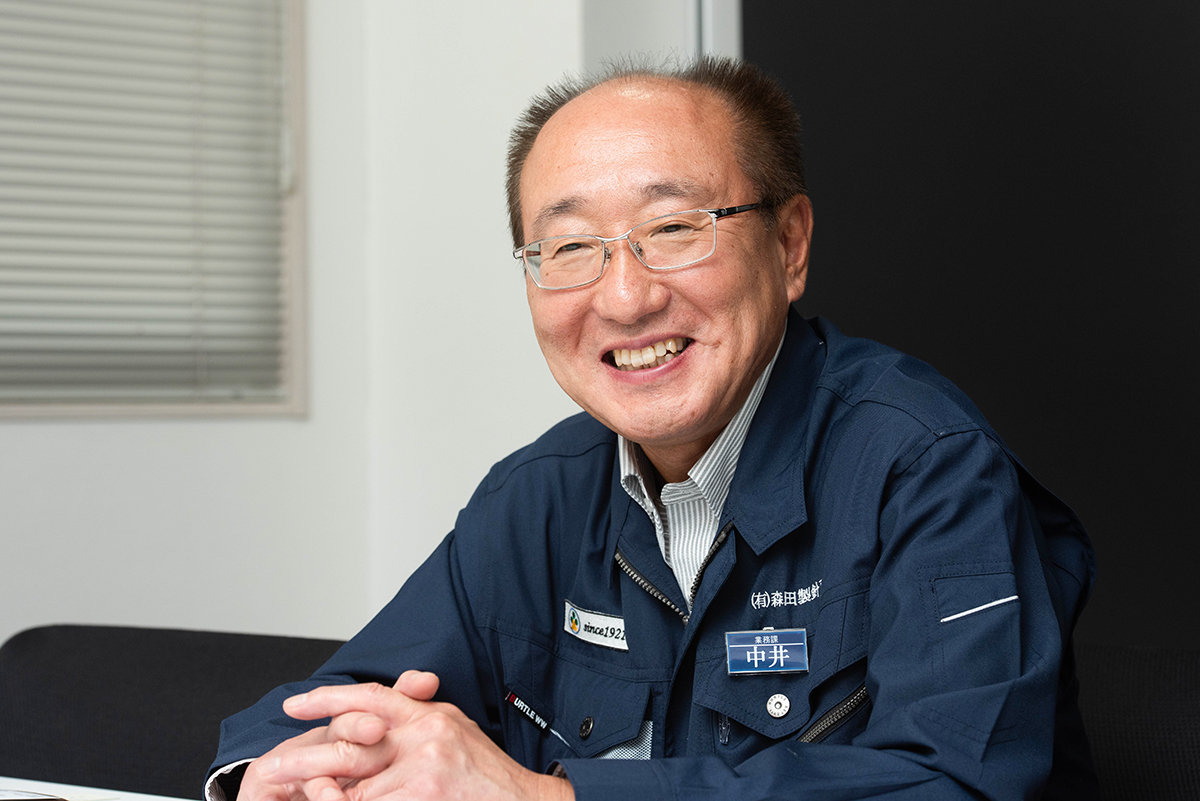
業務課係長 中井 達也氏
(取材・文/山口裕史 写真/福永浩二)