厚物のワイヤー放電加工に挑み続ける
ワイヤー放電加工は、電極の役割を果たす真ちゅう製のワイヤーをピンと張って、糸のこぎりのようにして対象となる鋼材に差し込み、電流の力で切断する方法だ。ワイヤーの直径は0.05~0.3mmほどで切断面と接触するうちにだんだんと細ってゆくので、厚みが40cm以上の鋼材では奥に進むほどに繊細な制御が求められる。
また、都度発生する削りかすをノズルから発する液圧できれいに取り除いていくのも経験がものをいう世界だ。三共精機では、最大74cmの厚みを持つ鋼材の切断も可能で、業界でも数少ない厚物に特化した放電加工に強みを持つ。

一枚目の写真の鋼材を横から撮影
1981年の創業時は家電業界向けの金属加工でスタートしたが、生産拠点の海外シフトで仕事が減り、新たな顧客として重電や自動車業界を開拓する。特に発電所関連に使われるタービンブレードは1500℃超という燃焼環境下で使われるため「ねばくて、堅い」耐熱鋼が材料に使われる。こうした難削材の切断を得意とするのがワイヤー放電加工だ。同社ではその時期にオーダーメードのワイヤー放電加工機を導入し、タービンブレードなどに使われる厚物のワイヤー放電加工へと軸足を移していった。
薄物のワイヤー放電加工は競合がひしめき価格競争を強いられる一方、厚物は舞い込んでくる受注こそ少ないが、利益の高い仕事が得られる。「あえて魚の少ない釣り堀に糸を垂らしている」と細川氏。最近でも大手二輪メーカーがモトクロスバイクのフレームの切削をするのに「やっと求めていた加工業者を見つけることができた」と喜ばれたという。政府系の研究機関のプラント、大手重工メーカーや建機メーカー、自動車メーカーからの試作品、試験片など受注は一品ものばかりだ。
また、同社は短納期も強みにしている。それを可能にしているのがベトナム人技術者だ。「土日や夜の時間帯に主に彼らに勤務してもらうことで、例えば金曜日に入った注文も土日の間に納品できる態勢を整えている」という。
2011年3月に起きた東日本大震災は、同社の事業に影を落とした。同社が得意とする発電所向けの仕事量が減ってしまったのだ。また、新たな柱として育てていた航空機部品を今度はコロナ禍の逆風が襲った。かといって手をこまねいているわけではない。
現在は、あらゆる金属加工の仕事をこなしながら、コロナ禍収束後は、得意とする厚物のワイヤー放電加工で、1mの厚物に挑もうとしている。「これからもよそがやらないことでうちらしさを追求していきたい」。
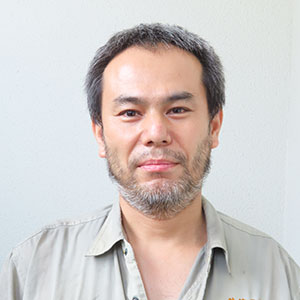
細川 修司氏
(取材・文/山口裕史)